Titanium Dioxide Uses
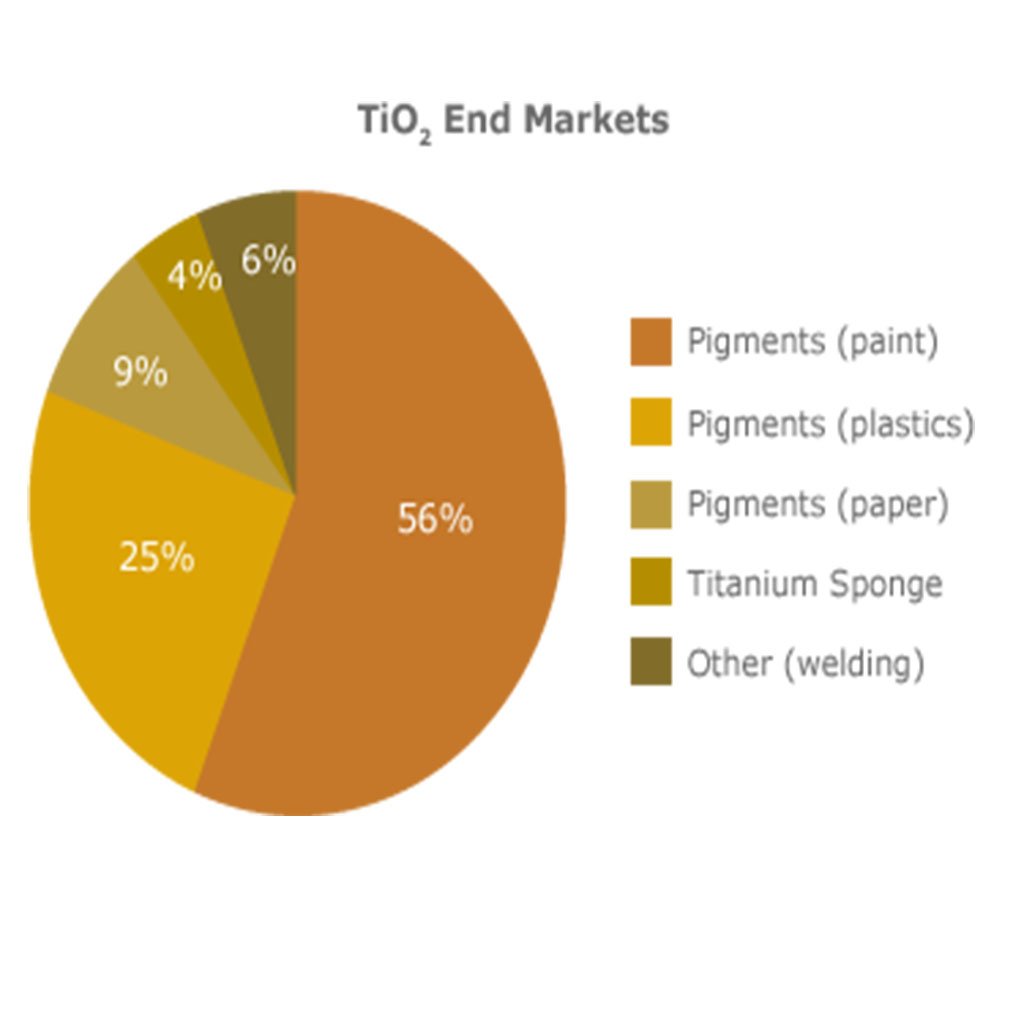
Titanium dioxide (TiO2) is the most widely used white pigment, for example in paints. It has high brightness and a very high refractive index. The light passes through the crystal slowly and its path is substantially altered compared to air.
If you have many small particles orientated in different directions, a high refractive index will lead to the scattering of light as not much light passes through. In lenses, high refractive index means high clarity and high polarizing power.
Titanium dioxide has a higher refractive index than diamond and there are only a few other substances that have a higher refractive index. Cinnabar (mercury sulfide) is an example. Historically, cinnabar was used as a red pigment.
Titanium Dioxide Uses for White Pigment
Titanium Dioxide uses are numerous. Four million tons of pigmentary TiO2 are consumed annually. Apart from producing a white colour in liquids, paste or as coating on solids, TiO2 is also an effective opacifier, making substances more opaque. Here are some examples of the extensive range of applications:
- Paints
- Plastics
- Papers
- Inks
- Medicines
- Most toothpastes
- Skimmed milk; adding TiO2 to skimmed milk makes it appear brighter, more opaque and more palatable.
Titanium Dioxide Uses in Plastics
The plastic industry is the second largest user of titanium dioxide.
As for the application of Titanium Dioxide in plastic products, besides its high covering power, high lightening power, and other pigment performance, it can also enhance the heat resistance, light resistance and weather resistance of plastic products, protecting plastic products from invasion of UV Rays, improving the mechanical capacity and electrical performance of plastic products.
Since the films of plastic products are much thicker than the coatings of oil paints and printing inks, they do not require high pigment volume concentration, plus it has high covering power and tinting strength, so the average amount used is usually 3% – 5%.
It is used in almost all thermosetting and thermo plastic plastics, such as polyolefins (mainly low-density polyethylene), polystyrene, ABS, polyvinyl chloride, etc. It can mix not only with dry resin powder, but also with liquid containing plasticizer. Another way of application is to process titanium dioxide into color master batch first, and then take it into use.
The particle sizes of most titanium dioxides for plastic are small. Generally, the particle size of titanium dioxide for coating is 0.2~0.4μm, while the particle size of titanium dioxide for plastic is 0.15~0.3μm.
Titanium Dioxide Uses in Sunscreens
Almost every sunscreen contains titanium dioxide. It is a physical blocker for UVA (ultraviolet light with wavelength of 315–400 nm) and UVB (ultraviolet light with wavelength of 280–315 nm) radiation. It is chemically stable and will not become decolourised under UV light.
TiO2 particles have to be coated with silica or alumina. This is because TiO2 particles that come into contact with water produce hydroxyl radicals which are potentially carcinogenic. The silica or alumina coating prevents the titanium dioxide particles from coming into contact with the skin and with water making titanium dioxide very safe to use.
Addition to cement and tiles
Titanium dioxide can be added to the surface of cements, tiles and paints to give the material sterilising, deodorising and anti-fouling properties. This is because the photocatalytic properties of TiO2 mean that, in the presence of water, hydroxyl free radicals are formed which can convert organic molecules to CO2 and water and destroy microorganisms.
Self-cleaning glass
In 2001, the first self-cleaning glass was brought onto the market. This type of glass is coated in a thin layer of transparent anatase. To make the coating, anatase is first combined with an organic complexing agent consisting of organic molecules which can act as ligands and bind to the titanium ion with co-ordinate bonds. This process is necessary to convert the titanium dioxide powder into a more soluble form so that it can be spread over the glass surface evenly. Once the coating is applied, the glass is heated to burn off the organic complexing agent, leaving the anatase coating.
The cleaning process works in two phases:
- Photocatalytic breaking down of dirt.
- Washing off breakdown products when it rains.
Anatase absorbs UV light with wavelengths close to the visible spectrum. This activates the titanium dioxide by exciting electrons to higher energy levels. The activated titanium dioxide reacts with water to generate hydroxyl radicals which break down organic molecules. The hydroxyl free radicals on the surface of the titanium dioxide increase the hydrophilic (‘water-loving’) character of the glass. When it rains, the water runs off the glass in the form of a sheet and the dirt is washed off. The water sheet leaves almost no streaks and the glass looks clean.